2.5 Retrofitting
Retrofitting is the strategy used to enhance capabilities of machine. By adding sensors, the team can generate insights of a machine or a production process in an indirect manner, improving their initial capabilities.
Background: typical retrofitting scenario
In many production sites is common to see very expensive and old assets which have been part of the factory for many years. Generally these assets are pacemakers, with high material output and producing 24/7. Due to its criticality, expensive and specialized maintenance services are paid to external service providers (e.g., machines Original Equipment Manufacturer - OEM) that travel from other countries once or twice per year. These machines are not connected to any network, have ancient HMIs and KPIs are registered manually by the operator or supervisor.
Sometimes these machines are standard ones (mass production by OEM), where the lack of capability for modifying the HMI or establishing communication with other machines restrict tailoring. Also, this can be the other way around, as very customized, but outdated machines to the actual necessities of the production team can be detrimental.
Factory leaders can not invest in new machines due to exorbitant fixed costs. At its best, the machines are upgraded (e.g., modern hardware and software installed) in intervals which are longer than 5 years.
Example of these types of machines:
- Hydraulic press
- Machining (e.g., CNC mill, turning)
- Industrial furnaces
- Standard machines (e.g., robotic arms)
- Customized machines (e.g., machine developed to produce a particular part number)
What is retrofitting?
Retrofitting is the strategy to enhance the capabilities of these type of assets. There are two main forms of retrofitting:
- Functional retrofit: upgrading the machine by swapping the existing hardware and software for a newer version. This can also be achieved by installing new actuators. This type of retrofit can be seen as an active approach, which straightly impacts the machine functionality.
- Retrofit from the IIoT perspective: adding sensors without altering and modifying the machine (particularly the machine certification). The main purpose is only to extract data. This passive approach serves as a first step of digitizing the asset and obtaining the production KPI’s in an automated and digital manner. United Manufacturing Hub only focuses in this type of retrofit.
Retrofit goal is to increase productivity and reduce cost, as you can see in the following image:
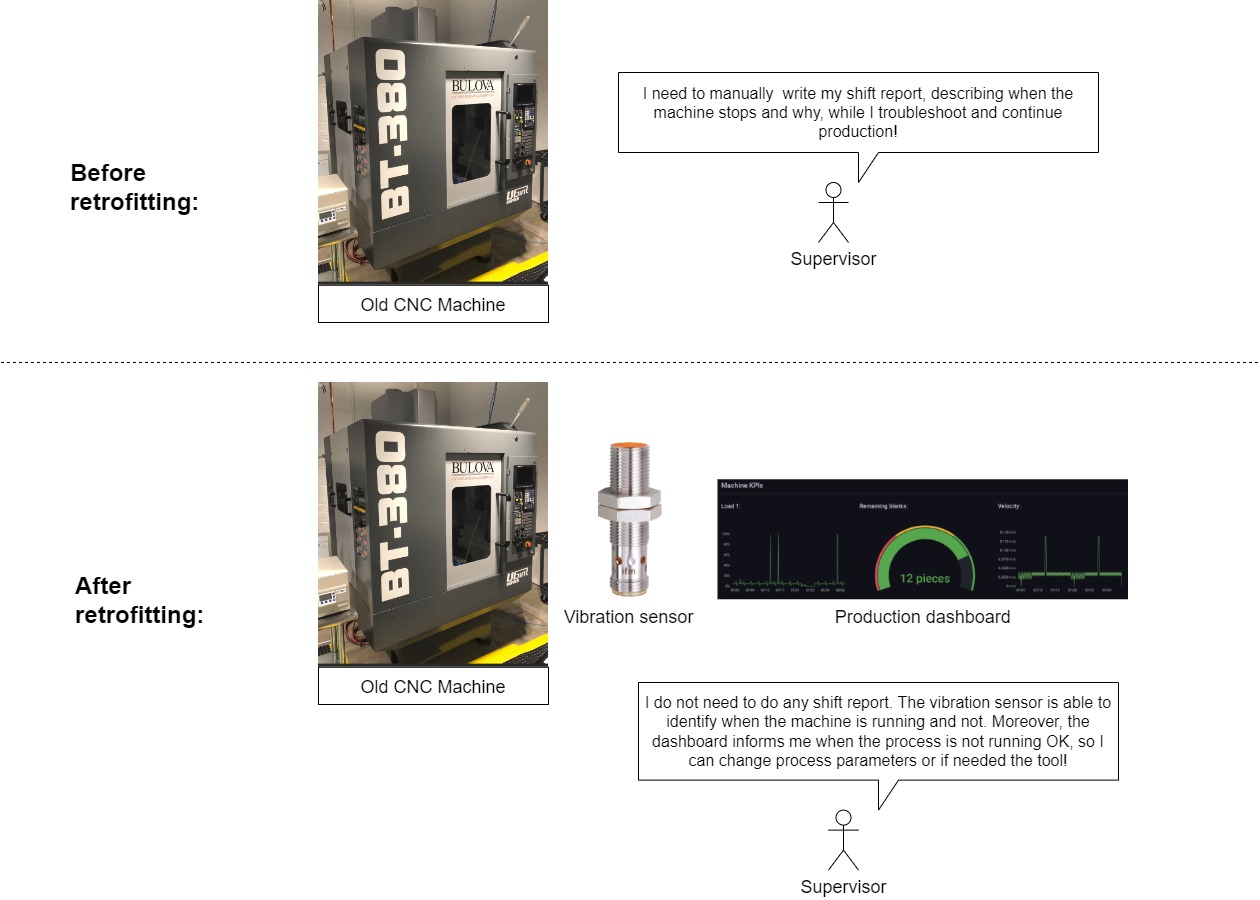
Where to do retrofitting?
In aged (without digital capabilities), expensive and critical production assets, which are forecasted to be utilized in the upcoming years.
When to do retrofitting?
Retrofitting is advised if one of the following scenarios is true:
- Machine is the bottleneck of the value chain and has outdated hardware and software, which makes it impossible to extract data
- Asset doesn’t have enough production capacity and these inputs are mostly given by manual processes (e.g., annotations from the operator)
- Exorbitant maintenance service fees
- Costly consumables such as hydraulic oil, coolant, lubricant
- Assets consume great amount of energy supply (electricity, water, propane, H₂, N₂)
How to do retrofitting? (examples)
- Maintenance and consumables cost reduction: change paradigm from preventive maintenance to diagnostic maintenance. Install sensors of temperature, viscosity to measure quality of the oil and reduce preventive maintenance tasks.
- Reduce services consumption by improving production planning: install sensors in order to measure the consumption of electricity, water and/or gas (e.g., propane, N2, H2, O2). Initiate projects for reducing costs by improving production planning, meaning only consume the services when production is happening.
- Pareto analysis of principal causes of stoppages. Define how can it be measured with sensors so data can be obtained. Data can be used as input to the production team, which can perform analyses and define corrective and preventive actions.
How to get started?
Define the most important KPI’s and/or the problem you want to address. Then, together with your team, map all the variables that interact with the machine. Propose (and brainstorm) examples of sensors that can help you obtain the data you need to measure the relevant indicator. An approach could be like the following diagram:
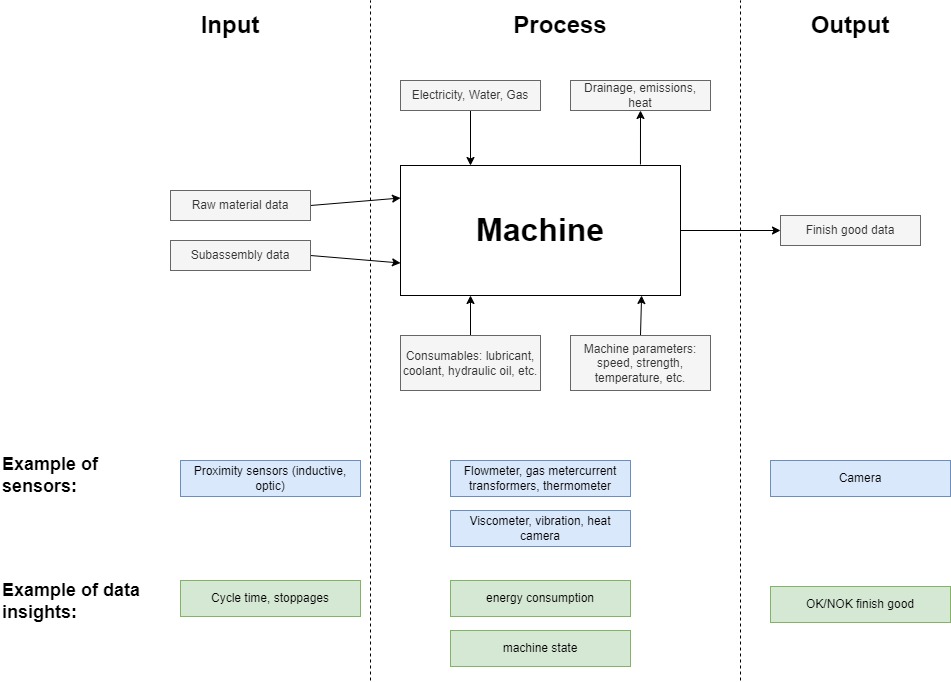
Afterwards, work on a “sensor plan”, where you can define which type of sensors, characteristics and the necessary hardware is needed (e.g., electricity sockets, cables, position in the machine, maintenance).
What’s next?
United Manufacturing Hub has plenty of experience retrofitting assets. An isolated use case is the first step to continue the digital transformation path to a connected shop floor. Please continue with further sections in the IIoT world.
Sources and further materials
Last modified February 17, 2023:
update (#208) (ea731fc)